De voordelen van magnesiumoxide-koolstofstenen zijn:weerstand tegen slakkenerosie en goede thermische schokbestendigheid.Het nadeel van MgO-Cr2O3-stenen en dolomietstenen was in het verleden dat ze slakbestanddelen absorbeerden, wat resulteerde in structurele afbrokkeling, wat tot voortijdige schade leidde.Door grafiet toe te voegen, hebben magnesiumkoolstofstenen deze tekortkoming geëlimineerd.Het kenmerk is dat de slak alleen in het werkoppervlak doordringt, zodat de reactielaag beperkt is tot het werkoppervlak, de structuur minder afbladdert en een lange levensduur heeft.
Naast de traditionele asfalt- en harsgebonden magnesiumoxide-koolstofstenen (inclusief gebakken, met olie geïmpregneerde magnesiumoxide-stenen),de magnesiumoxide-koolstofstenen die op de markt worden verkocht, zijn onder meer:
(1) Magnesia-koolstofstenen gemaakt van magnesiumoxide met 96% ~ 97% MgO en grafiet 94% ~ 95% C;
(2) Magnesia-koolstofstenen gemaakt van magnesiumoxide met 97,5% ~ 98,5% MgO en grafiet 96% ~ 97% C;
(3) Magnesia-koolstofstenen gemaakt van magnesiumoxide met 98,5%~99% MgO en 98%~C grafiet.
Volgens het koolstofgehalte zijn magnesiumoxide-koolstofstenen onderverdeeld in:
(I) Gebakken, met olie geïmpregneerde magnesiumoxidebakstenen (koolstofgehalte minder dan 2%);
(2) Met koolstof gebonden magnesiumoxidestenen (koolstofgehalte minder dan 7%);
(3) Magnesia-koolstofsteen gebonden met kunsthars (koolstofgehalte is 8%~20%, in enkele gevallen tot 25%).Antioxidanten worden vaak toegevoegd aan asfalt/harsgebonden magnesiumoxide-koolstofstenen (het koolstofgehalte is 8% tot 20%).
Magnesia-koolstofstenen worden geproduceerd door hoogzuiver MgO-zand te combineren met geschubd grafiet, roet, enz. Het productieproces omvat de volgende processen: vermalen van grondstoffen, zeven, sorteren, mengen volgens het ontwerp van de materiaalformule en de prestaties van het product, volgens de combinatie De temperatuur van het middeltype wordt verhoogd tot bijna 100 ~ 200 ℃ en wordt samen met het bindmiddel gekneed om de zogenaamde MgO-C-modder (groen lichaamsmengsel) te verkrijgen.Het MgO-C moddermateriaal met behulp van synthetische hars (voornamelijk fenolhars) wordt in koude toestand gegoten;het MgO-C moddermateriaal gecombineerd met asfalt (verwarmd tot een vloeibare toestand) wordt in een hete toestand (bij ongeveer 100°C) gevormd.Afhankelijk van de batchgrootte en prestatie-eisen van MgO-C-producten kunnen vacuümtrillingsapparatuur, compressievormapparatuur, extruders, isostatische persen, hete persen, verwarmingsapparatuur en ramapparatuur worden gebruikt om MgO-C-moddermaterialen te verwerken.naar de ideale vorm.Het gevormde MgO-C-lichaam wordt in een oven bij 700 ~ 1200 ° C geplaatst voor een warmtebehandeling om het bindmiddel om te zetten in koolstof (dit proces wordt carbonisatie genoemd).Om de dichtheid van magnesiakoolstofstenen te vergroten en de hechting te versterken, kunnen ook vulstoffen die lijken op bindmiddelen worden gebruikt om de stenen te impregneren.
Tegenwoordig wordt kunsthars (vooral fenolhars) meestal gebruikt als bindmiddel voor magnesiumoxide-koolstofstenen.Het gebruik van kunstharsgebonden magnesiakoolstofstenen heeft de volgende basisvoordelen:
(1) Milieuaspecten maken de verwerking en productie van deze producten mogelijk;
(2) Het proces van het produceren van producten onder koude mengomstandigheden bespaart energie;
(3) Het product kan worden verwerkt onder niet-uithardende omstandigheden;
(4) Vergeleken met teerasfaltbindmiddel is er geen plastische fase;
(5) Een verhoogd koolstofgehalte (meer grafiet of bitumineuze steenkool) kan de slijtvastheid en de slakweerstand verbeteren.
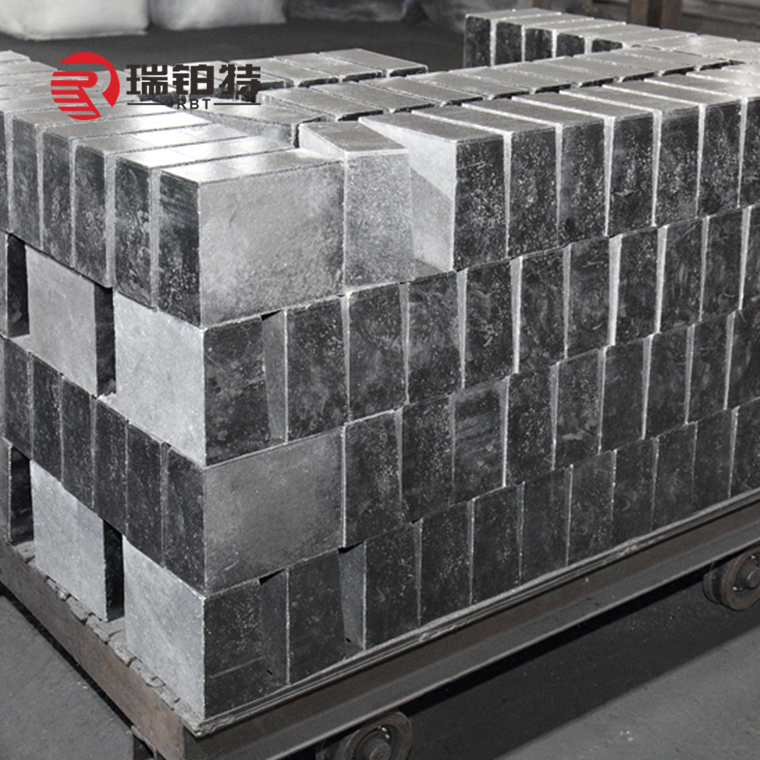
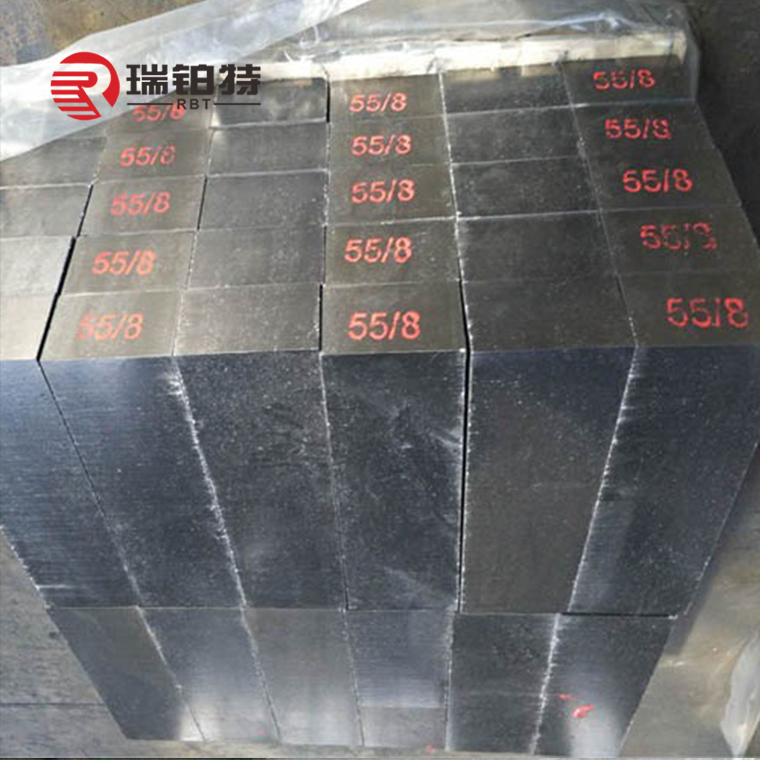
Posttijd: 23 februari 2024